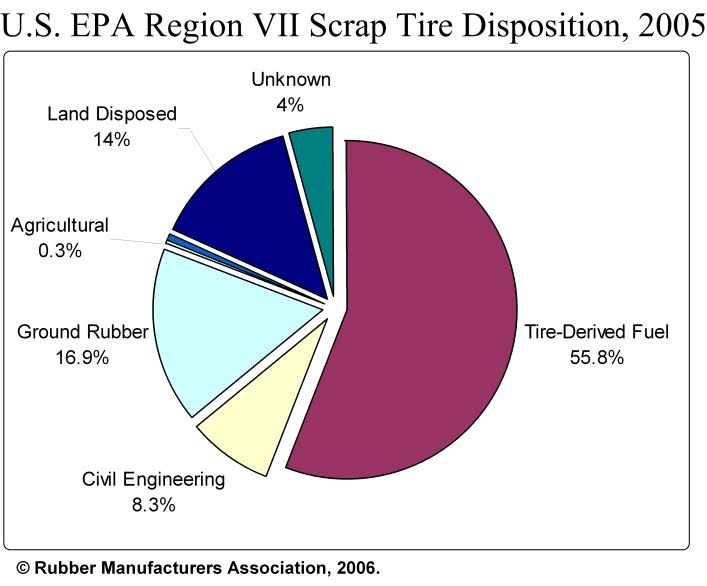
Sixty percent of the rubber consumed in the United States today is used to make tires. In 2008, 290 million new tires were shipped for use by cars and trucks. Of these, 80 percent were for passenger cars and 20 percent were for trucks. In addition, 20 percent were “original equipment” tires and 80 percent replaced used tires. While scrap tire stockpiles have been reduced by 87 percent since 1990 there were still 303.2 million scrap tires generated in 2000. Two thirds of these tires were from passenger cars and the remainder came from trucks, heavy equipment, aircraft, off-road and scrapped vehicles.
Scrap tires present unique recycling and disposal challenges because they are heavy, bulky and made from a variety of materials. More than half of recovered scrap tires are used as tire-derived fuel (TDF), which is a low-sulfur, high heating value fuel. Scrap tires can be recycled as whole or split tires, or as crumb (ground) or shredded rubber. Whole tires are used for artificial reefs and playground equipment; split tires for floor mats, belts, and dock bumpers; crumb rubber for mudguards, carpet padding, tracks and athletic surfaces, and rubberized asphalt; shredded tires for road embankment or highway fill material. Civil Engineering applications, which include their use in asphalt rubber mixes, accounts for 8.3% of the overall disposition of scrap tires.
There are two main methods of incorporating Ground Tire Rubber (GTR) into asphalt:
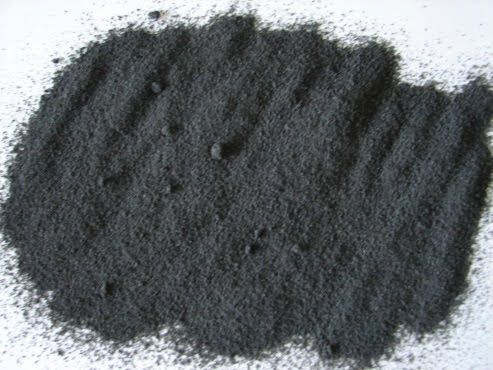
Wet Process – The GTR is first combined with the asphalt binder and digested before this modified asphalt is used to create the HMA. There are two types of wet process, terminal blend (or ‘wet process no agitation’) and wet process high viscosity.
Dry Process – the GTR is used to replace a fraction of the aggregate within the HMA. (The dry process has a very poor performance record and has not seen much use in the past twenty-five years. Therefore, no additional information regarding the dry process is included.)
The primary use of crumb rubber modified asphalt binders in pavement applications include crack and joint sealants; binders for chip seals, interlayers, and hot-mix asphalt (including dense-, gap-, and open-graded gradations); and membranes.
Rubberized Asphalt Concrete (RAC)
Rubberized asphalt concrete (RAC) is a road paving material made by blending GTR with asphalt to produce a binder which is then mixed with conventional aggregate materials (wet process). This mix is then placed and compacted into a road surface. There are two primary types of binders for RAC, asphalt-rubber and terminal blend.
Asphalt-rubber is defined by the American Society for Testing and Materials (ASTM) Standard D6114 as “a blend of paving grade asphalt cement, ground recycled tire (that is, vulcanized) rubber and other additives, as needed, for use as binder in pavement construction. The rubber shall be blended and interacted in the hot asphalt cement sufficiently to cause swelling of the rubber particles prior to use.” The asphalt-rubber binder is field blended (at the hot mix plant) and requires specialized mobile mixing equipment to produce. Typical crumb rubber modifier (CRM) content for asphalt-rubber ranges from 18-22 percent. The crumb rubber modifier used in asphalt-rubber is in the 10-16 mesh range.
Terminal blends are binder materials that use finely ground (30 mesh or smaller) crumb rubber as an asphalt cement/binder modifier and are typically blended at the asphalt refinery. Terminal blended binders contained less than 20 percent crumb rubber modifier (typically in the 10-12% range) and have been used successfully in Florida for more than 30 years and California for more than 20.
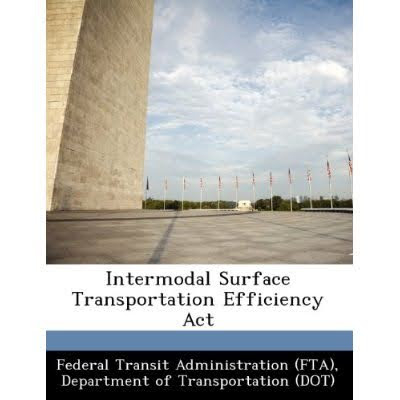
Use of CRM in hot-mix asphalt increased substantially in the early 1990s due in large part to the mandate imposed in ISTEA. A survey of state highway administrations conducted by AASHTO in January 1993 indicated that 21 states, including Virginia, used CRM in hot-mixes in 1992. VDOT experimented with a variety of asphalt rubber mixes and processes on several projects across the state during this period. The production processes tried were difficult, costly (due in part to small quantities produced), and the few sites paved had varied performance. The lack of success and repeal of the ISTEA mandate led VDOT to abandon the effort and no crumb rubber modified asphalt has been placed in Virginia for more than twenty years until recently.
While most states, like Virginia, turned away from the use of CRM, several did not. Arizona, California, Florida, and Texas have all developed and refined crumb-rubber modified binders and it is regularly used in hot-mix asphalt in those states (Arizona’s first hot-mix asphalt containing asphalt rubber was placed in 1975). Arizona DOT and local governments in Arizona use asphalt rubber binder in both open-graded and gap-graded hot-mixes. However, open-graded friction courses using asphalt rubber binders are the most popular used by the Arizona DOT. California DOT and local governments in southern California use asphalt rubber in dense-, gap-, and open-graded hot-mix asphalt. Texas DOT uses asphalt rubber primarily in a gap-graded mixture identified as coarse matrix, high binder mix (CMHB).
Florida DOT has used the terminal blending process for modifying its asphalt cements/binders since the mid 1970’s. Typically 6-12% by weight of asphalt binder of a fine ground rubber is used in dense- and open-graded hot mixtures.
Quiet Pavements Open the Door for Asphalt Rubber
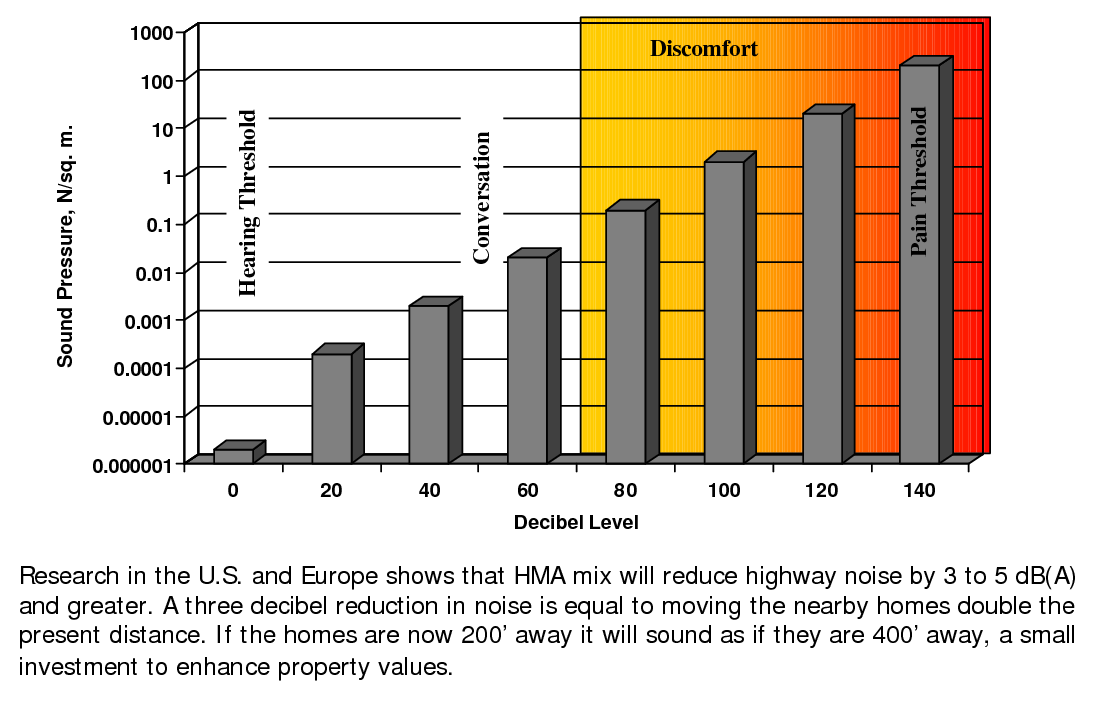
Research in the U.S. and European Open-Graded Friction Course (OGFC) mixes will reduce highway noise by 3 to 5 dB (A) with asphalt rubber modified binder mixes having superior noise reduction to conventional binders. To the average person, this reduction is the same as doubling the distance between the source of the noise and their location. When comparing the noise reduction that is possible by choosing asphalt pavement-up to 7 dB(A) -we see how much more practical pavement surface selection is than construction of noise barrier walls.
The decrease in noise levels of rubber modified OGFC has sparked a renewed interest in asphalt rubber binder use in Virginia and VDOT has begun to construct asphalt pavements using GTR modified asphalt mixes. In 2011, VAA members produced GTR OGFC and (Stone Matrix Asphalt (SMA) asphalt mixes on Quiet Pavement test section projects in the Leesburg, Richmond and Williamsburg areas. In 2012, VAA members produced additional rubber-modified asphalt for projects in the Fairfax, Marshall and Fredericksburg areas. Each of these projects is part of research studies to quantify the benefits Quiet Asphalt technology and to evaluate the performance of GTR in asphalt mixes.
Today, VAA, VDOT and Virginia asphalt contractors are conducting joint efforts to utilize GTR in other mixes used on VDOT projects as an alternative to polymer modification. The ultimate goal is to produce a mixture that provides superior performance at a lower cost. Research conducted by other agencies has shown the value of these mixes. At the NCAT Test Track in Auburn, Alabama, asphalt mixtures containing GTR are being evaluated and compared to other non-GTR mixes. This not only will reduce the initial and long-term cost of the pavement, but has significant environmental impacts through the reduced demand on new asphalt binders and reduction in landfilled materials.