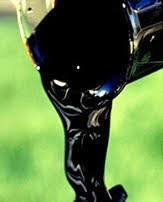
Asphalt (sometimes called “liquid asphalt”, “asphalt cement” or “asphalt binder”) is a sticky, black and highly viscous liquid or semi-solid form of petroleum. It may be found in natural deposits or may be a refined product; it is a substance classed as a pitch. Asphalt occurs naturally in a few places in the world, but most of the asphalt used today for paving comes from petroleum crude oil. Asphalt is the heaviest part of the crude—what’s left after all the volatile, light fractions are distilled off for products such as gasoline. Refined asphalt is graded for specific engineering properties and can be liquefied in three ways.
- By heat, this is what happens at an asphalt concrete plant (known as “asphalt cement” or “asphalt binder”) Click here to go to the Asphalt Cement/Binder page.
- By blending it with a light petroleum solvent (known as “cutback asphalt” or “cutback”)
- By suspending it in water through the emulsification process (known as “emulsified asphalt” or “asphalt emulsion”)
Cutback asphalt and emulsified asphalts are called liquid asphalts to distinguish them as a group from normal asphalt cement/binder. This page discusses basic information on these liquid asphalts and their use for “tack” and “prime” applications.
Cutback Asphalt
Cutback asphalt is simply a combination of asphalt cement and petroleum solvent. Some are thin enough to be used as prime oil or tack, while others must be heated for use. Their uses included dust control, pavement maintenance, construction (chip seal) and cold mix patching.
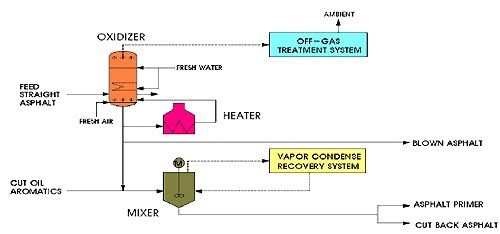
Petroleum solvents used for dissolving binder are sometimes called distillate, diluent, or cutter stock. If the solvent used in making the cutback asphalt is highly volatile it will quickly escape by evaporation. Solvents of lower volatility evaporate more slowly. On the basis of relative speed of evaporation, cutback asphalts are divided into three types:
- Rapid-Curing (RC) – asphalt and a volatile solvent or light distillate, generally in the gasoline or naphtha boiling point range.
- Medium-Curing (MC) – asphalt and a solvent of intermediate volatility or medium distillate, generally in the kerosene boiling point range.
- Slow-Curing (SC) – asphalt and an oily diluent of low volatility Slow-curing (SC) asphalts are often called road-oils. This term originated in earlier days when asphaltic residual oil was used to give roads a low-cost, all-weather surface. . (At present, SC is not used in Virginia.)
The degree of fluidity obtained in each case depends on the grade of asphalt cement/binder, volatility of the solvent, and proportion of solvent to binder. The degree of fluidity results in several grades of cutback asphalt. Some are quite fluid at ordinary atmospheric temperatures and others are somewhat more viscous and may require heating to melt them enough for construction operations. Cutback asphalts can be used with cold aggregates, with a minimum of heat. RC and MC types of cutback asphalts are used in a variety of highway construction. Among the more important uses are road mixing operations, stockpiling mixes, and spray applications such as prime.
The specifications for cutback asphalt are in Section 210 of the VDOT Road and Bridge Specifications.
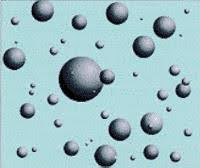
Emulsified Asphalts
Asphalt Emulsions consist of microscopic particles of asphalt cement coated with a mild soap solution to form homogenous, water-based asphalt. Emulsions can be either anionic (negatively charged) or cationic (positively charged). These emulsions are further classified into slow setting, medium setting and rapid setting categories. Choice of emulsion type is determined by its intended purpose. Since emulsions are water based, they are environmentally friendly yet subject to temperature changes. Emulsions are used for many applications in fog seals, chip seals, slurry seals, pavement repair and in construction.
In the emulsification process, hot asphalt cement/binder is mechanically separated into minute globules and dispersed in water treated with a small quantity of emulsifying agent. The water is called the continuous phase and the globules of binder are called the discontinuous phase. The machine used in this process is a colloid mill; the binder globules are extremely small, mostly in the colloidal size range. By proper selection of an emulsifying agent and other manufacturing controls, emulsified asphalts are produced in several types and grades.
By choice of emulsifying agent, the emulsified asphalt may be:
- Anionic – binder globules are electro-negatively charged.
- Cationic – binder globules are electro-positively charged.
Also, by variation in materials and manufacture, emulsified asphalts of both anionic and cationic types are made in several grades. Some of these grades and their uses are:
- Anionic – Non-Virginia grades RS-2 tack and seal coat, SS-1h slow set slurry and tack
- Cationic – Virginia grades, CRS-2 tack and seal coat, CRS-1 tack, CRS-1h tack, CSS-1h two types for slurry (rapid set and slow set) and tack; CMS-2 prime, tack, seal, and cold mix.
Because particles having a like electrostatic charge repel each other, asphalt globules are kept apart until the emulsion is deposited on the surface of the soil or aggregate particles. At this time, the asphalt globules coalesce through neutralization of the electrostatic charges or water evaporation. Coalescence of asphalt globules occurs in rapid and medium setting grades, resulting in a phase separation between asphalt and water. When this coalescence occurs, it is usually referred to as the break or set.
Emulsified asphalts can be used with cold as well as heated aggregates, and with aggregates that are dry, damp, or wet.
The specifications for emulsified asphalts are in Section 210 of VDOT’s Road and Bridge Specifications.